A wide range of test benches dedicated to vehicle, powertrain, engine and associated components
Tests related to engines (combustion, micro-hybrid, hybrid, electric) of complete vehicles or their components (powertrain or other component) require different bench technologies (eddy current brake, dynamic brake, with inertia) in various configurations: chassis dyno benches, powertrain and e-powertrain benches, engine benches, engine component benches, characterization benches...
A test bench is a set of equipment set up in a room generally controlled in temperature and humidity. It can be very simple in the case of an elementary engine function test, or very complex in the case of real operation simulation of a powertrain or a complete vehicle.
Our R&D department dedicated to the design of benches has a strong expertise in this field having already designed many benches for our internal needs (powertrain bench, e-motor bench, ElectroMagnetic Compatibility bench, etc.) and to cover our customers' needs.
Our bench testing services can have several objectives. It can be for:
- Development testing: calibration - fine tuning (optimal adjustments to be made after a first pre calibration conception phase), calibration of engine control systems, qualification of the performance of components or of complete engines. The aim is to validate the technical solutions proposed and developed in terms of design, thermodynamics, material resistance and durability.
- Certification or homologation testing (normative aspect): checking that the vehicle complies with pollution standards and specifications in terms of consumption and power.
- Validation and control testing (quality aspect): qualification of powertrain or component durability, accelerated ageing testing and/or reliability testing, specific durability cycles...
Climatic chassis
dynamometer
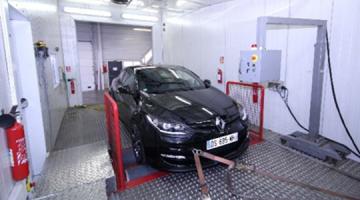
- Iso-speed characterizations
- Performance, Consumption, Emission control
- Cold start (HW definition/calibration)
- Spark plug fouling
- Vehicles cycles
- VHL cycles with simulated driving conditions
- Heat up
- Climatic validation
Climatic
engine test bench
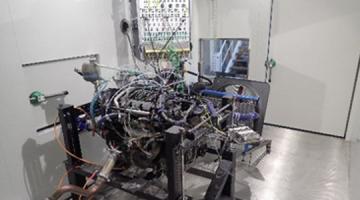
- Running-in, full load curves
- Cold start
- Friction losses study (with ancillary pumps)
- Characterization
- Heat up
- Calibration (energy and component development)
- Thermal validation of electric motor
- Independent fluid control: air, water, oil, EGR, Water CAC
Dynamic calibration test bench
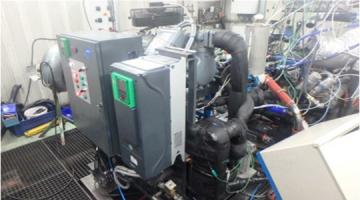
- Energy and component development
- Characterization of functions
- Durability cycles
- Running-in, Full load curves
- Knock
- OBD
Durability engine bench - Heavy Duty Applications
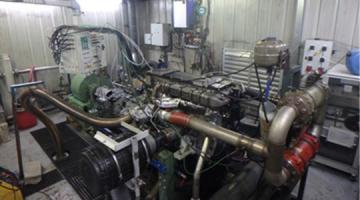
- Mechanical development
- Characterization of functions
- Gearbox ratio imposition on cycle
- Running-in, Full load curves
- Durability Cycles
- OBD
Durability engine test bench - Thermal shock
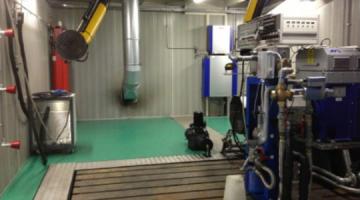
- Rapid variation of temperatures
- Characterization of functions
- Water and engine oil
- Durability cycles
Overview of some of our benches
Dynamic bench for electric, hybrid or combustion powertrains
This dynamic test bench (entirely realized by our R&D Department) allows to test a great number of possible combinations without being constrained by the entire structure of the vehicle. To meet the challenges of developing ever cleaner and more energy-efficient vehicles, the powertrain test bench is made to run: thermal, light (48V) or heavy (high voltage) hybrid or all-electric engines.
This flexibility of our bench allows us to respond quickly to the development and tuning needs of car manufacturers and equipment suppliers. Thus, the durability or development tests carried out on this test bench make it possible to validate the chosen architectures in terms of mechanical reliability, pollution and consumption.
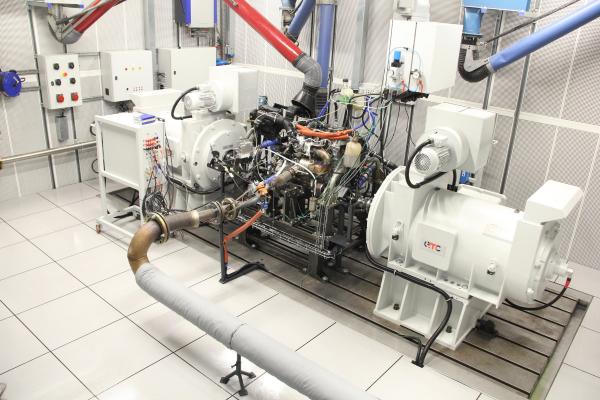
Example of our dynamic bench 'B9' - 2 units
Performance of the dynamic bench
- 2 reversible generators with a sum power of 400 Kw
- Independent speed control of each generator
- Driving in rpm, torque or vehicle speed mode
- Fast monitoring (500Hz acquisition)
- Fluid conditioning (air, fuel, glycol, oil, etc...)
- PULSAR control and acquisition software especially design for the powertrain simulator bench
- Complies with the manufacturers requirements of the vibration levels.
Options
- Gas analysis system: 5 gas analysis bay + EGR
- Particule analysis system: Pegasor
- Fumimeter – Opacimeter
- LMS or SONAR vibration measurement station
- Battery simulator (if required)
- Cold Group Thermal Shock (fluids if required)
Machines / generators
- Maximum torque 2000 Nm from 0 to 1000 RPM for each generator
- Maximum speed 3000 RPM
- Maximum power 200 Kw from 1000 RPM to 3000 RPM
- The direction of rotation is fully reversible manually and automatically
Fluid conditioning
- Fuel conditionner
- Air temperature and hygrometry
- Temperature and pressure control of oil and water
- AVL consumption scale
Measurement and control
- PULSAR control and acquisition
- Manual and automatic control of the test bench
- Fast acquisition 500hz
- Combustion analysis system: Osiris, Indicom
- ETAS equipment with motor control connection, lambda meter
- Vibration measurement (optional)
Electric Powertrain Bench Configuration (epowertrain only):
100kW 600A /600V Simulator and DC Load Machines:
Rated speed | NM | A | kW | rpm | Hz | Const. Power Speed (rpm) |
1532 | 2338 | 953 | 359 | 1532 | 500 | 2800 |
e-motor high dynamic bench, climatic option (Eclair)
This high dynamic bench is an internal development of our research department. Dedicated to characterization and durability tests on electric motors and with an optional climatic chamber, this Eclair test bench achieves high performance in speed, torque and power in a controlled climatic environment.
This bench supports the increasing demand for testing electrified components in the automotive and aeronautical industries.
A high-performance speed-torque-power combination.
With a total power of 270kW, a speed of up to 21krpm and a torque of 510Nm up to 6000rpm, the high performance of the ECLAIR dyno allows it to test more than 90% of existing and future EV designs. This test facility covers the characterization and validation steps of electrified traction chains or electrical components.
Achieving high performance, this bench is equipped with a battery simulator (250kW / 1000V / 1000A), a high precision wattmeter (WT3000E), a precision torque meter (range 1000 Nm 22 000 rpm : HBM T12HP), a CAN VECTOR card or ETAS equipment with motor control link (INCA).
The Eclair bench is extremely versatile
- Adaptability to all protocols - CANs - Flexray etc...
- All types of adaptable cycles
- Continuous vibration monitoring
- Possibility to use the Back to Back bench in addition for durability tests
Characteristics of the Eclair bench
Dynamic bench 1 machine
- Full power: 270kW
- Torque regime: 21krpm and 510Nm to 6000rpm (up to 21 000 rpm)
Climatic condition
- Ambient air: -45°C to +120°C
- Water or oil: -30°C to +120°C, cold group thermal shock (fluids as required)
Acquisition
- PULSAR (EMC): Fast acquisition 5000hz, for the control and monitoring of the bench (10khz on specific values via power meter (WT3000E))
- PULSAR VIBE (EMC): Vibration acquisition, 50kHz on 8 channels for vibration monitoring and LMS station for post-processing and characterization
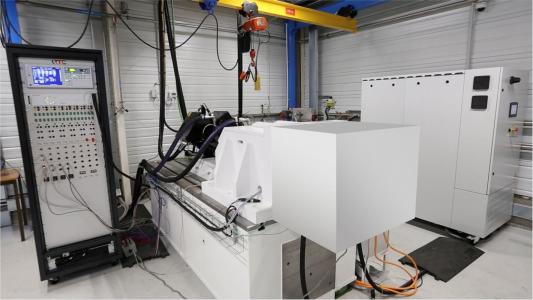
- Battery simulator 250kW / 1000V / 1000A
- Precision torque measurement 1000 Nm 22 000 rpm range : HBM T12HP
- VECTOR CAN card or ETAS equipment with motor control link (INCA)
Electric powertrain and transmission dynamic bench
This type of dynamic bench with double machine allows to characterize complete electric powertrain (eGMP) but also gearboxes or for combustion engine (and hybrid and micro-hybrid) the mechanical gearbox.Depending on the way this bench is set up, the transmission devices or devices associated to the modification of vehicle kinematics can be characterized.
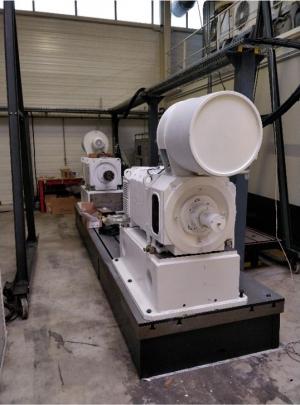
Torquemeter x2
- Manufacturer - Model: HBM T40B-3 kNm
- Precison: +/- 3 Nm
- Nominal torque: 3000 Nm
- Maximum allowable torque: 4500 Nmm
Battery simulator
- Power: 100kW
- Input voltage: 3x 400V AC
- Output voltage: 0-600V
- Output current: 0-600A
Characteristics of the high dynamic bench
- Cell area 52 m2
- Generator/motor (x2) ABB DMA280L32V
- Power: 2x369 KW
- Max. torque: 2238 Nm (Max. torque from 2238 Nm @1500 rpm à 1000 Nm @2800 rpm)
- Max. speed: 2800 rpm
- Filter box 500Kvar
- Battery simulator I-TS-3870-600-100
- PULSAR control software
Acquisition stem
- Pressure: 6 input
- Temperature: 16 inputs for K type thermocouple and 16 inputs for PT100
- Measurements: 26 BNC (16x 0-10V, 10x 4-20mA)
- Torque: 2 torque + 1 measurements
- Power supply: 8x 24V (20A) and 8x 12V (50A)
- Control: 12x 4-20mA
High dynamic component bench (e-machine 48V)
This high dynamic bench allows the characterisation of components such as the realisation of a complete cartography of a starter-alternator (48V) of the real torque realised in order to recalibrate the cartography values.
First developed for the aeronautics sector, it is more particularly dedicated to high speed 48V applications, especially in the automotive sector.
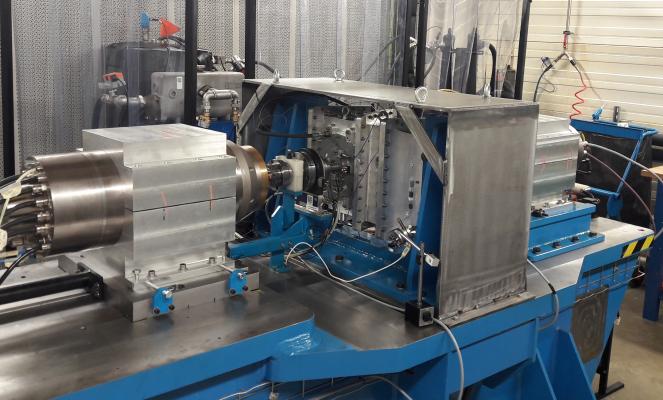
Characteristics of the high dynamic bench
- Cell area 27 m2
- Fisher motor e-machine 100kW / 18000rpm / 79Nm
- Fisher generator e-machine 70kW / 24000rpm / 60Nm
- 2 x KEB inverters 250kW
- 2 x MAYR ROBA-DS coupling
- Pulsar Lite control software
- PULSAR VIBE vibration monitoring software
- air circulation system in the cell
- Ice water cooling system for engine and accessories cooling
- Oil conditionning system for the lubrication of the specimen
Torquemeter x2
- Manufacturer - Model: HBM T40-100Nm
- Precison: +/- 0,1%
- Nominal torque: 100 Nm
High frequency acquisition system
- Manufacturer - Model: PXI National Instruments chassis
- Acquisition frequency: 600 kHz
Acquisition system
- PULSAR LITE software
- Measurements inputs: 16 AI 4-20 mA / 16 AI O-10V / 8 freq inputs / 8 counter inputs
- Temperature: 32 thermocouple inputs
- Control output: 16 A0 0-10V
- Inputs / Outputs 24V : 16 DI 24V / 16 DO 24V
- PULSAR VIBE software
- Measurements inputs: 14 accelerometer inputs / 6 AI 0-5V
- Control outputs: 6 A0 0-5V
- Inputs / Outputs 24V: 4 DO 24V
Battery cycling benches
Our cycling benches are dedicated to durability and characterization tests for batteries in development (design and validation) for an optimal efficiency (life cycle, ageing, power, performance, lifetime) as well as for thermal cycling tests required by the ECE R100 (annex 8B). They allow to test batteries dedicated to the automotive sector for tests campaigns combining charge and discharge cycle at a constant temperature or with thermal cycle.
Technical characteristics of our battery cycling benches
Model 1
- Admissible dimensions of the tested batteries:
o Width: 1,4 m
o Lenght: 2,0 m - Thermal characteristics of the chamber
-40°C / +85°C (limitation for safety) - Thermal management of fluids (glycol / oil)
-35°C/+95°C (limitation for safety) - Kratzer simulator 250kW /1000A /1000V
- CAN BMS-VECTOR monitoring system
- Dedicated controller for safety limits and runaway management.
- Isolated thermocouple channels 1000V (150+)
- Dynamic DC profile (WLTP, RDE,...)
- 2 CAN buses
- DAQ 2MHz for transient tests
Model 2
- Chamber Thermal characteristics
-30°C / +55°C - Thermal management of fluids (glycol / oil)
-30°C/+70°C - Kratzer simulator 250kW /1000A /1000V
- CAN BMS-VECTOR monitoring system
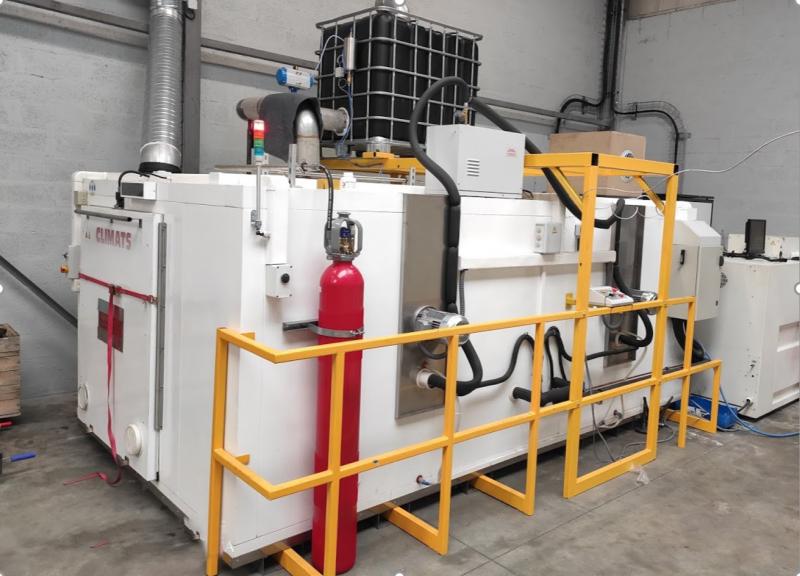
Climatic test cells with their chassis dyno for vehicle testing
A climatic test cell with its climatic chassis dyno allows us to simulate and reproduce the environment of a vehicle. We are equipped to test 2, 3 and 4-wheel vehicles.
Rolling tests can be carried out in extreme temperature ranges (cold rolling with high temperature) as well as cold start with high temperature tests.
Testing can be implemented to meet the needs of our customers in terms of validation and/or development of a product or function.
These test facilities can also be used to carry out tests on sub-assemblies in accordance with manufacturers' standards and specifications (e.g. CL08 tests according to PSA standard B21 7130)
Test context in key words: soaking, isovitesse, characterization, performance, consumption, engine depollution, cold start (exploitation, calibration), catalyst ageing, driving cycles, real drive emissions, climatic validation...
Climatic dyno bench - Achères site
Dyno performance
- Max speed 160km/h (grille ventilation max 130km/h)
- Absorbed torque at the wheels 2700Nm (7000N tangential force at the tyres)
- Mechanical power input in continuous 150kW
- Measurement of torque, speed and roller distance with HBM torque meter type T40
- Quadricycles: 4x2 two-wheeled bench (traction or propulsion)
- Bicycles/Tricycles: specific mounting for contact on 1 roller - customised radiator ventilation
Performance of the associated climatic chamber
- Temperature range from -35°C to +50°C
- Cooling capacity:
o 80kW to -30°C
o 160kW to -15°C - Heating power: 20kW
Climatic chamber with loading facility - Osny site
- MAHA twin roller dynamometers 160kW, speed up to 120km/h
- Temperature range from -30°C to +55°C
- Double compressor 46Kw of cold power at 30°C
- 6Kw heating resistor
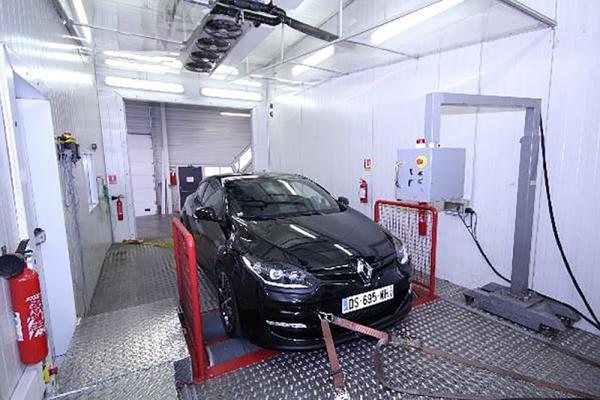
Chassis dyno for vehicle emission tests (Emission pollution - EURO 6, WLTP...)
Our chassis dyno allows us to implement the pollutant emission measurements as defined in the EURO 6 standards and measurements procedures (and also WLTP).
Our chassis dyno meets the precision and reproducibility requirements of emissions measurements allowing vehicles to be tested under accurately simulated road conditions while remaining within the laboratory. The chassis dyno must exceed the demanding performance criteria required by US EPA, FTP 75 / SFTP (US06) EUDC directives (accurate road law simulation, fast inertia simulation response and critically damped to provide realistic powertrain load, accurate synchronization of multi-roller systems to ensure road-like conditions...)
Our facility allows us to control the temperature and hydrometry within the test chamber. It offers the possibility to change the force applied to the wheels, allows to control the radiator grill ventilation, is equipped to measure the pollutants emitted and/or to quantify the electrical autonomy of the vehicle (via a dilution system and gas analysis bays), allows tests at constant speed but also to run different cycles (WLTC, American cycles, Japanese cycles...).
Our main bench is for light vehicles (Thermal, Hybrid, Electric) or LDV (Light Duty Vehicle) which includes the M1 and N1 categories (with the possibility of approving N2 vehicles following the deviations). With recent measurement protocols such as Euro 6, measurements on chassis dynamometers are supplemented by measurements in real driving conditions RDE, measurements with PEMS.
Chassis dyno emissions measurement - Osny site
Bench description and associated instrumentation
- Real-time computer operating system: Morphée 2
- Zöllner 2-wheel drive bench 186 kW, maximum speed 200 km/h
- Car ventilation speed up to 160km/h
- Temperature from 12 to 40°C with regulated hygrometry
- Constant volume sampler with adjustable sample from 1 to 12m3/min
- 1 Diluted gas analyzer 6 Gases: CO, CO2, NOx, O2, HC, CH4
- 1 Normative particle analyzer (AVL Particle Counter)
- Normative measurement with two sets of 4 bags and continuous measurement
In addition
- Use of 2 raw material analyzers with EGR sample
- Particle measurement by class: Cambustion DMS500
- Programming of all offline tests (road law, cycle, gear shift law)
- Rapid CO/CO2 analyser
- Gas analyser: NH3, NO, NO2
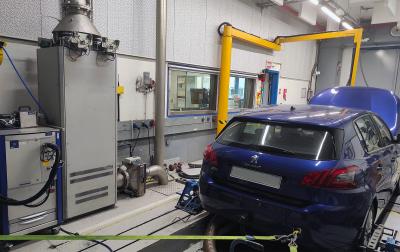
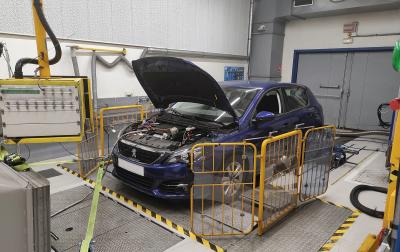
PEMS (Portable Emission Measurement System) pour des mesures RDE (Real Driving Emissions)
In the context of Euro 6 approvals and future developments, a series of requirements must be satisfied, including measurements of pollutant emissions (gaseous pollutants and particles) based on laboratory measurements of exhaust emissions (using the WLTC cycle) supplemented by measurements of emissions under real driving conditions (RDE) carried out by a (PEMS)
Measurements in real-life driving conditions allow the correlation of pollutant emissions between the measurements made in the laboratory for the homologation cycle and the vehicle driven on the road every day.
The RDE tests are performed on open roads. These tests follow the different stages of the WLTC cycle. They must therefore begin with an urban section, followed by an out-of-town section and a freeway section. The tests in real driving conditions are carried out on roads with an altitude of less than 700 meters and temperatures between 0°C and 30°C.
All greenhouse gas and pollutant emissions are measured during an RDE test, but only NOx emissions are discriminating. Thus, for Euro 6d full, NOx emissions must not exceed 1.5 times the permissible emissions for a vehicle approved under this standard.
Note that in the context of Euro 6 homologation (and its future variations), RDE measurements are also required for ISC measurements.
This test is for vehicles already on the road that must also have remained compliant with emissions regulations. These tests are mandatory for all registrations as of January 1, 2019 and for all new registrations as of September 1, 2019.
The manufacturer must guarantee the conformity of the vehicle with the homologation data for a minimum of 5 years or 100,000 km, whichever comes first. In-service conformity refers to laboratory and real driving gas emission tests and evaporation tests.
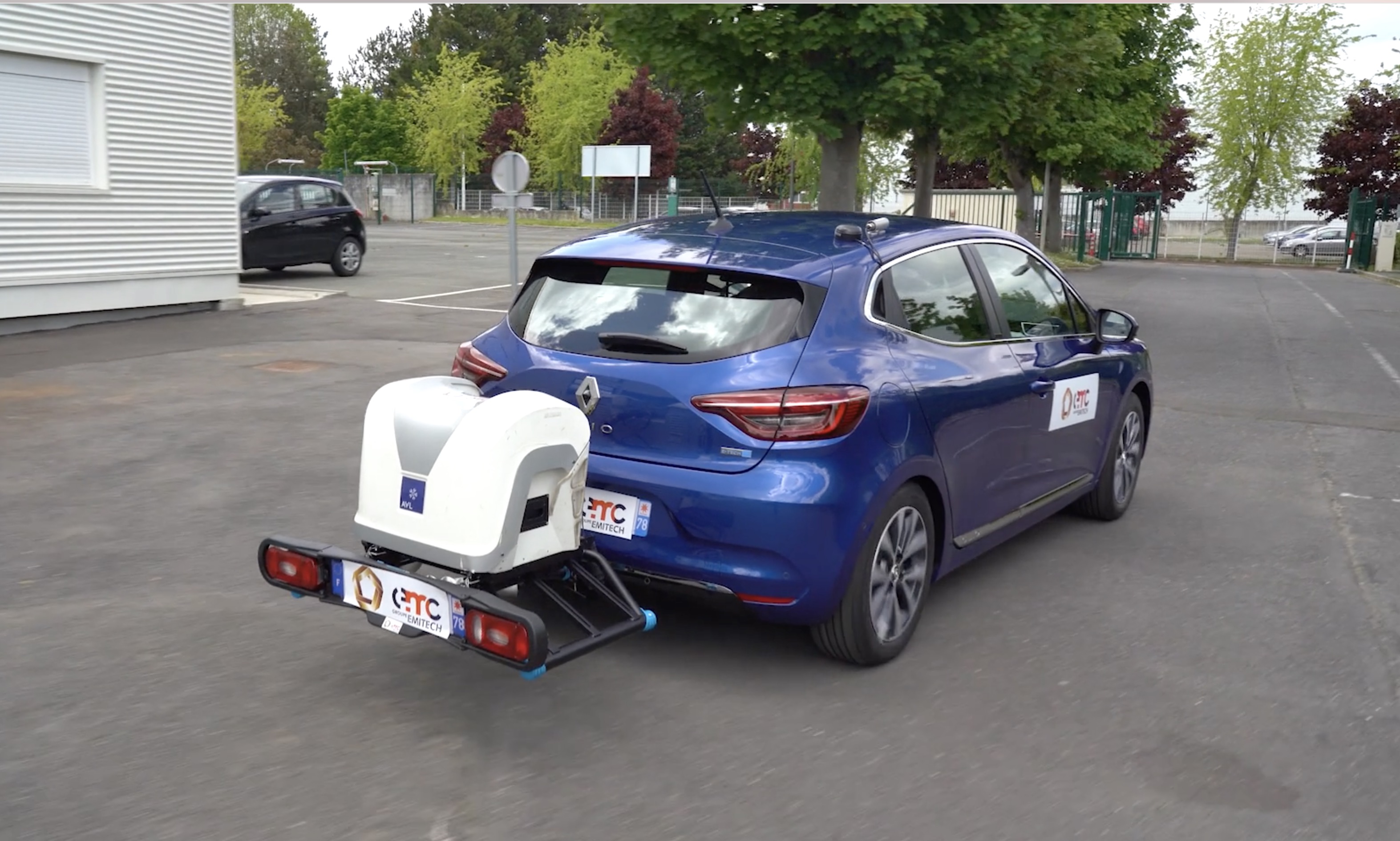
Which bench for which use
The test benches for testing vehicles and their various components (complete powertrain or sub-assemblies) are almost as numerous as the parameters to be optimized for a more efficient mobility.
Find below our different types of benches
Climatic sector |
|||
---|---|---|---|
High capacity climatic roller test bench (Air -30 to +60°C) |
Dynamic |
180 kW |
- |
High capacity climatic roller test bench (Air -30 to +55°C) |
Dynamic |
160 kW |
- |
Climatic roller test bench (Air -30 to +50°C / fluids on request) |
Dynamic |
230 kW |
1000 Nm |
Climatic roller test bench (Air -30 to +50°C / fluids on request) |
Dynamic |
220 kW |
1000 Nm |
Mechanical and energy sector |
|||
Chassis dyno |
Dynamic |
144 kW |
460 Nm |
2 chassis dyno |
Dynamic |
220 kW |
460 Nm |
Chassis dyno |
Dynamic |
230 kW |
1000 Nm |
Chassis dyno |
Dynamic |
300 kW |
500 Nm |
Chassis dyno |
Stationary |
130 kW |
270 Nm |
Chassis dyno |
Stationary |
230 kW |
750 Nm |
3 chassis dyno |
Stationary |
300 kW |
500 Nm |
2 chassis dyno |
Stationary |
294 kW |
900 Nm |
Chassis dyno |
Stationary |
300 kW |
900 Nm |
Chassis dyno |
Stationary |
590 kW |
4000 Nm |
PWT / ePWT chassis dyno (Max couple from 2000 Nm @1000 rpm at 640 Nm @3000 rpm) - More |
Dynamic |
2x200 kW |
2000 Nm |
Multi-purpose test bench aeronautics, propeller engine |
Stationary |
- |
1600 Nm |
Emission sector |
|||
High capacity climatic roller test bench (Air -30 to +60°C) - More |
Dynamic |
186 kW |
- |
Components sector |
|||
Electric test bench - 2 machines (48V) (Max. couple from 70 Nm @12000 rpm at 53 Nm @18000 rpm / 60 Nm @11000 rpm at 28 Nm @24000 rpm) - More |
High dynamic |
100 kW / 70 kW |
70 Nm / 60 Nm |
e-PWT or transmission (Max. couple from 2238 Nm @1500 rpm at 1000 Nm @2800 rpm) - More |
Dynamic |
2 x 369 kW |
2238 Nm |
Electric bench with climatic option (Max. couple 510 Nm - Max. speed 22000 rpm) - More |
High dynamic |
270 kW |
570 Nm |
ElectroMagnetic Characterization of Electric Motor (Max. couple 510 Nm - Max. speed 21000 rpm) |
High dynamic |
270 kW |
510 Nm |
Battery cycling bench - More |
- |
- |
- |
Battery abuse test bench (deformation, crushing, impalement) |
- |
- |
- |
Fuel pump characterization bench |
- |
- |
- |
Water pump characterization bench |
- |
- |
- |
Altitude test bench |
- |
- |
- |
Altitude simulation test bench |
- |
- |
- |
Engine architecture |
|||
---|---|---|---|
Combustion analysis (combustion characterization, knocking robustness, combustion efficiency...; engine internal aerodynamic development, combustion model recalibration) |
Stationary bench |
||
Mise au point (MAP) de déshuilage (MAP de géométrie de déshuileurs et caractérisation de leur efficacité) |
Banc stationnaire |
||
Production conformity (running-in, full load curves) |
Stationary bench |
||
Vibration characterization (vibration measurements on engine components, e.g. alternator, to identify vibration levels and frequencies; operational deformation on powertrain; operational deformation of exhaust line; transfer function on vehicle) |
Stationary bench |
||
Thermal characterization (thermal balance: measurement of the energy introduced by the fuel and of all useful and lost energy; thermo management: optimization of the heating of an engine with control of one or more thermostats; engine thermometry or engine function) |
Statioary bench |
||
Special fuels tests (knocking calibration; dedicated export engine calibration; robustness of pollution control devices for special fuels; accelerated aging of pollution control devices) |
Stationary bench |
||
Exhaust Gas Recirculation (EGR) system development (Implementation and tests on gasoline or diesel EGR systems, super-cooled or not) |
Stationary bench |
||
Friction losses measurements (Average friction pressure in combustion: engine friction measurement in combustion with influence of load, crankshaft misalignment...; Average friction pressure in driven: complete engine friction measurement or station to station; Average friction pressure in thermal transient: friction losses measurements in driven station to station or in fire on the stabilized points of a cycle, in thermal transient) |
Mixed bench (braking & driving) |
||
Characterization of functions in steady state (characterization of distribution drives, measurements of instantaneous cuts of distribution drives...) |
Stationary bench |
||
Characterization of functions in transient regime (response time and turbo pumping, lubrication circuit in high transient ... ; Development of turbocharger, characterization of e-turbo, measurement of oil consumption of a turbo and its permeability) |
Dynamic bench |
||
Characterization of the lubrication circuit (permeability of the oil circuit, measurement of pressures at different points) |
Mixed bench (braking & driving) |
||
Characterization of the oil consumption |
Mixed bench (braking & driving) |
||
Engine calibration - Gasoline & Diesel |
|||
Function calibration (strategy of response to throttle off: injector recalibration, turbo maintenance...; pre-calibration of approval before driving) |
Dynamic bench |
||
Calibration of functions (combustion noise on temperature rise; injection calibration with validation of injector mapping; pollution control; tuning of comfort/noise/reliability; tuning of air loop for turbo adaptation; tuning of EGR; tuning of DPF: particle filter regeneration; tuning of full-load and dynamic performance; cutting structure tuning; changeover to a new fuel; Sensitivity curves: back pressure, temperature after exchanger, etc.) |
Stationary bench |
||
Function calibration (CMF calibration: friction mapping validation; CSE positioning / pollution control) |
Mixed bench (braking & driving) |
||
Engine calibration (measurement of parameters: consumption, pollution, PMF... on driving cycles) |
Dynamic bench |
||
Engine architecture |
|||
Endurance and reliability of the complete engine (validation of the engine equipped with the Stop & Start function; simulation of driving cycle according to the profile provided: vehicle and road cycle data, speed and gear engaged according to time, etc.) |
Dynamic bench |
||
Endurance and reliability of the complete engine (thermal shocks; road cycle, urban cycle...; measurement of wear evolution; gumming; seizing; lubrication; continuous full load; idle; overspeed) |
Stationary bench |
||
Endurance and reliability on components (tests of sensitive components in transitory: turbos, particle filters...) |
Dynamic bench |
||
Endurance and reliability on components (alternator; balance shaft; exhaust manifold; turbo corrosion; timing belts; Exhaust Gas Recirculation fouling; injector fouling; catalyst aging; oil aging; coolant aging) |
Stationary bench |
||
Emission post-treatment |
|||
Development and characterization of components (catalyst; DeNox: Nox trap, SCR; particulate filter: efficiency, clogging, regenerability study...) |
Stationary bench |
||
Complete vehicle - Roller benches |
|||
Endurance and reliability (catalyst ageing, particulate filter durability, clutch performance, vehicle/engine/organ validation - cylinder head/injector clogging cycles) |
Roller bench |
||
Thermal or climatic (Validation tests on alternators in a hot environment on different road cycles) |
Roller bench |
||
Cold starting, start-up |
Roller bench |
||
Validation of engine control functions (OBD) on WLTC cycles (and other) |
Roller bench |
||
Emission or anti-pollution tests (according to standardized cycle) |
Emission chassis dyno |
||
Stabilized tests (according to standardized cycle) |
Emission chassis dyno |
||
Performance characterization |
Emission chassis dyno |
Stationary test benches |
---|
Endurance / Reliability tests
|
Engine architecture characterization tests
|
Engine control function calibration tests |
Stationary test benches |
Endurance / reliability test
|
Engine architecture characterization tests
|
Engine control functions calibration tests in dynamics
|
Roller bench |
Climatic tests
|
Functional diagnosis tests
|
Endurance / reliability tests
|
Emission chassis dyno |
Pollution tests
|
Stabilized tests
|
Performance tests
|